
Non-contact infrared thermometers allow engineers to obtain accurate temperature measurements in applications where it is impossible or very difficult to use
any other kind of temperature sensor.
In some cases, this is because the application itself literally destroys a contact-type sensor, such as when using a thermocouple or
resistance temperature detector to measure molten metal. If the electrical interference is intense, such as in induction heating, the electromagnetic field surrounding the object will cause inaccurate results in conventional sensors. A remote infrared thermometer is immune to both problems.
For maintenance, no other sensor is able to provide long-distance, non-contact temperature measurements needed to find hot spots or trouble areas in distillation columns, vessels, insulation, pipes, motors or transformers. As a maintenance and troubleshooting tool, it's difficult to beat a handheld laser thermometer.
Infrared temperature sensors range from relatively inexpensive infrared thermocouples, to sophisticated, computer-based linescanners. In between is a wide variety of handheld and permanently mounted IR measuring systems that meet just about any temperature monitoring need imaginable.
Infrared Thermocouples
An infrared thermocouple is an unpowered, low-cost infrared thermometer that measures surface temperature of materials without contact. It can be directly installed on conventional thermocouple controllers, transmitters and digital readout devices as if it were a replacement thermocouple. An infrared thermocouple can be installed in a fixed, permanent location, or used with a handheld probe.
Because it is self-powered, it relies on the incoming infrared radiation to produce a signal via thermoelectric effects. Therefore, its output follows the rules of radiation thermal physics, and is subject to nonlinearities. But over a given range of temperatures, the output is sufficiently linear that the signal can be interchanged with a conventional thermocouple.
Although each infrared thermocouple is designed to operate in a specific region, it can be used outside that region by calibrating the readout device accordingly.
Pyrometers or Radiation Thermometers
Pyrometers, as they are sometimes called come in a variety of configurations. One option is a handheld display/control unit, plus an attached infrared probe. The operator points the probe at the object being measured and reads the temperature on the digital display.
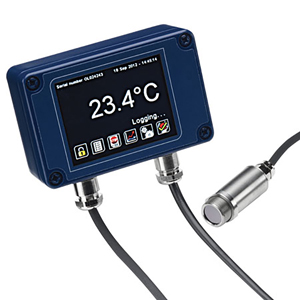
These devices are ideal for making point temperature measurements on circuit boards, bearings, motors, steam traps or any other device that can be reached with the probe. The inexpensive infrarred thermometers are self-contained and run off battery power.
Other pyrometers are handheld or mounted devices that include a lens similar to a 35mm camera. They can be focused on any close or distant object, and will take an average temperature measurement of the laser "spot" on the target that fits into its field of view.
Handheld pyrometers are widely used for maintenance and troubleshooting, because a technician can carry one around easily, focus it on any object in the plant, and take instant temperature readings of anything from molten metals to frozen foods.
When mounted in a fixed position, these infrared thermometers are often used to monitor the manufacturing of glass, textiles, thin-film plastic and similar products, or processes such as tempering, annealing, sealing, bending and laminating.
Fiber Optics Extensions
When the object to be measured is not in the line of sight of a infrared thermometer,
a fiber optic sensor can be used. The sensor includes a tip, lens, fiber optic cable, and a remote monitor unit mounted up to 30 ft away. The sensor can be placed in high energy fields, ambient temperatures up to 800°F, vacuum, or in otherwise inaccessible locations inside closed areas.
Two-Color Systems
For use in applications where the target may be obscured by dust, smoke or similar contaminants, or changing emissions as in "pouring metals," a
two-color infrared thermometer is ideal. It measures temperature independently of emissivity. Systems are available with fiber optic sensors, or can be based on a fixed or handheld configurations.
Linescanners
A linescanner provides a "picture" of the surface temperatures across a moving product, such as metal slabs, glass, textiles, coiled metal or plastics. It includes a lens, a rotating mirror that scans across the lens' field of view, a detector that takes readings as the mirror rotates, and a computer system to process the data.
As the mirror rotates, the line scanner takes multiple measurements across the entire surface, obtaining a full-width temperature profile of the product. As the product moves forward under the sensor, successive scans provide a profile of the entire product, from edge to edge and from beginning to end.
The computer converts the profile into a
thermographic image of the product, using various colors to represent temperatures, or it can produce a "map" of the product. The 50 or so measurement points across the width can be arranged in zones, averaged, and used to control upstream devices, such as webs, cooling systems, injectors or coating systems.
Linescanners can be extremely expensive, but they offer one of the only solutions for obtaining a complete temperature profile or image of a moving product.
Mounted Vs. Portable Infrared thermocouple
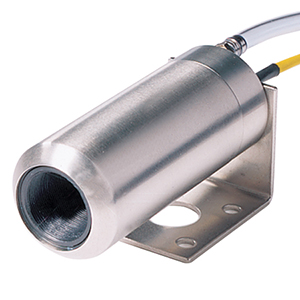
IR temperature measurement devices also can be classified as portable or permanently mounted. Fixed mount laser thermometers are generally installed in a location to continuously monitor a process. They often operate on AC line power, and are aimed at a single point. Measured data can be viewed on a local or remote display, and an output signal (analog or digital) can be provided for use elsewhere in the control loop.
Fixed mount systems generally consist of a housing containing the optics system and the IR detector, connected by cable to a remote mounted electronics/display unit. In some loop-powered designs, all the thermometer components and electronics are contained in a single housing; the same two wires used to power the thermometer also carry
the 4 to 20 mA output signal.
Battery powered, handheld infrared gun typically have the same features as permanently mounted devices, but without the output signal capability. Portable units are typically used in maintenance, diagnostics, quality control, and spot measurements of critical processes.
Portable devices include pyrometers, infrared thermometers and two-color systems. Their only practical application limit is the same as a human operator; i.e., the sensors will function in any ambient temperature or environmental condition where a human can work, typically 32-120°F (0-50°C).
At temperature extremes, where an operator wears protective clothing, it may be wise to similarly protect the instrument. In shirt-sleeve manufacturing or process control applications, handheld laser thermometers can be used without worrying about the temperature and humidity, but care should be taken to avoid sources of high electrical noise. Induction furnaces, motor starters, large relays and similar devices that generate EMI can affect the readings of a portable sensor.
Portable non-contact sensors are widely used for maintenance and troubleshooting. Applications vary from up-close testing of printed circuit boards, motors, bearings, steam traps and injection molding machines, to checking temperatures remotely in building insulation, piping, electrical panels, transformers, furnace tubes and manufacturing and process control plants.
Because an infrared sensor measures temperature in a "spot" defined by its field of view, proper aiming can become critical. Low-end pyrometers have optional LED aiming beams, and higher end infrared thermometers have optional laser pointing devices to help properly position the sensor.
Permanently mounted devices are generally installed on a manufacturing or process control line, and output their temperature signals to a control or
data acquisition system. Radiation thermometers, two-color sensors, fiber optics, infrared thermocouples, and linescanners can all be permanently mounted.
In a permanent installation, an instrument can be very carefully aimed at the target,
adjusted for the exact emissivity, tuned for response time and span, connected to a remote device such as an indicator, controller, recorder or computer, and protected from the environment. Once installed and checked out, such an instrument can run indefinitely, requiring only periodic maintenance to clean its lenses.
Infrared thermometers designed for permanent installation are generally more rugged than lab or portable instruments, and have completely different outputs. In general, systems that operate near a process are ruggedized, have NEMA and ISO industrial-rated enclosures, and output standard process control signals such as 4-20 mA dc, thermocouple mV signals, 0-5 Vdc, or serial RS232C.
For very hot or dirty environments, instruments can be equipped with water or thermoelectric cooling to keep the electronics cool, and nitrogen or shop air purging systems to keep lenses clean.
Why should I use an infrared thermometer to measure temperature in my application?
Non-contact IR thermometers allow users
to measure temperature in applications where conventional sensors cannot be employed. Specifically,
in cases dealing with moving objects ( i.e., rollers, moving machinery, or a conveyor belt), or where non-contact measurements are
required because of contamination or hazardous reasons (such as high voltage), where distances are too great, or where the temperatures
to be measured are too high for thermocouples or other contact sensors.
How to Choose an Infrared Thermometer
- Determine the field of view (target size and distance)
- Consider the type of surface being measured and its emissivity
- Analyze the spectral response for atmospheric effects or transmission through surfaces
- Specify the temperature range and the mounting needs
- Don't forget: response time, environment, mounting limitations, viewing port or window applications, and desired signal processing
What should I consider about my application when selecting an IR thermometer?
The critical considerations for any infrared thermometer include field of view (target size and distance), type of surface being measured
(emissivity considerations), spectral response (for atmospheric effects or transmission through surfaces), temperature range and mounting
(handheld portable or fixed mount). Other considerations include response time, environment, mounting limitations, viewing port or window
applications, and desired signal processing.
What is meant by Field of View, and why is it important?
The field of view is the angle of vision at which the instrument operates, and is determined by the optics of the IR sensor. To obtain an accurate
temperature reading, the target being measured should completely fill the field of view of the instrument. Since the infrared device determines
the average temperature of all surfaces within the field of view, if the background temperature is different from the object temperature,
a measurement error can occur. OMEGA offers a unique solution to this problem. Many OMEGA infrared thermometers feature patented laser switchable
from circle to dot. In the circle mode a built-in laser thermometer creates a 12-point circle which clearly indicates the target area being measured.
In the dot mode a single laser dot marks the center of the measurement area.
What is emissivity, and how is it related to infrared temperature measurements?
Emissivity is defined as the ratio of the energy radiated by an object at a given temperature to the energy emitted by a perfect radiator,
or blackbody, at the same temperature. The emissivity of a blackbody is 1.0. All values of emissivity fall between 0.0 and 1.0. Most infrared
thermometers have the ability to compensate for different emissivity values, for different materials. In general, the higher the emissivity of
an object, the easier it is to obtain an accurate temperature measurement using infrared. Objects with very low emissivities (below 0.2) can be
difficult applications. Some polished, shiny metallic surfaces, such as aluminum, are so reflective in the infrared that accurate temperature
measurements are not always possible.
How can I mount the infrared pyrometer?
The pyrometer can be of two types, either fixed-mount or portable. Fixed mount units are generally installed in one location to
continuously monitor a given process. They usually operate on line power, and are aimed at a single point. The output from this type
of instrument can be a local or remote display, along with an analog output that can be used for another display or control loop.
Battery powered, portable infrared ''guns'' are also available; these units have all the features of the fixed mount devices, usually
without the analog output for control purposes. Generally these units are utilized in maintenance, diagnostics, quality control,
and spot measurements of critical processes.
What else should I take into account when selecting and installing my infrared measurement system?
First, the instrument must respond quickly enough to process changes for accurate temperature recording or control. Typical response times for infrared thermometers are in the 0.1 to 1 second range. Next, the unit must be able to function within the environment, at the ambient temperature. Other considerations include physical mounting limitations, viewing port/window applications (measuring through glass), and the desired signal processing to produce the desired output for further analysis, display or control.
I want to measure the temperature through a glass or quartz window; what special considerations are there?
Transmission of the infrared energy through glass or quartz is an important factor to be considered. The pyrometer must have a wavelength where the glass is somewhat transparent, which means they can only be used for high temperature. Otherwise, the instrument will have measurement errors due to averaging of the glass temperature with the desired product temperature.
What is spectral response, and how will it affect my readings?
The spectral response of the unit is the width of the infrared spectrum covered. Most general purpose units (for temperatures below 1000°F) use a wideband filter in the 8 to 14 micron range. This range is preferred for most measurements, as it will allow measurements to be taken without the atmospheric interference (where the atmospheric temperature affects the readings of the instrument).
Some units use wider filters such as 8 to 20 microns, which can be used for close measurements, but are ‘‘distance-sensitive’’ against longer distances. For special purposes, very narrow bands may be chosen. These can be used for higher temperatures, and for penetrations of atmosphere, flames, and gases. Typical low band filters are at 2.2 or 3.8 microns. High temperatures above 1500°F are usually measured with 2.1 to 2.3 micron filters. Other bandwidths that can be used are 0.78 to 1.06 for high temperatures, 7.9 or 3.43 for limited transmissions through thin film plastics, and 3.8 microns to penetrate through clean flames with minimum interference.
If a part is moving, can I still
measure temperature?
Yes. Use infrared devices or direct
contacting sensors plus a slip ring
assembly.
Can a two-color infrared system
be used to measure low
emissivity surfaces?
Only if at high temperature, say,
above 700°C (1300°F).
What error will result if the spot
size of the infrared pyrometer is
larger than the target size?
It would be indeterminate. The
value would be a weighted average
that wouldn’t necessarily be
repeatable.